Because of the simple process and low price, traditional electron beam and thermal evaporation are widely used in the production of optical thin films. Thermal evaporation is generally applicable to film materials with a melting point lower than 1500deg. W \ TA \ Mo \ Nb \ Fe \ Ni \ Pt \ Cu and other materials are used as evaporation source materials. The film materials are placed on the evaporation source materials and heated to vaporize and overflow its atoms or molecules from the surface to form a steam stream, which is incident on the substrate surface and condensed into a solid film. The principle of electron beam evaporation is that after hot electrons are emitted from the filament, they are accelerated by the accelerating anode and get kinetic energy to bombard the evaporation material at the anode, so that the evaporation material is heated and vaporized to realize evaporation coating.
Electron beam evaporation can obtain much higher energy density than resistance heating source, thus evaporating high melting point materials; The film material is placed in the water-cooled copper crucible, which can avoid evaporation of the container material and reaction between the container material and the plating material, and improve the purity of the plating film; Heat directly acts on the surface of evaporation material, with high thermal efficiency and small loss of heat conduction and radiation.
Compared with other types of coating methods, the kinetic energy of the evaporation film material in the process of electron beam and thermal evaporation is relatively low, and the generated dielectric film layer will be porous, low density and columnar structure. On the one hand, because the film layer is porous, it absorbs water vapor and changes the refractive index of the film layer; The temperature and humidity of the storage environment or the use environment will bring changes in the spectral curve of the film. On the other hand, the low density structure reduces the mechanical properties of the film to some extent. This adverse effect is often eliminated by heating the substrate to a high temperature of several hundred degrees, but it cannot be completely eliminated. The process of heating also limits the type of substrate and introduces thermal stress in the film layer.
When the cost is considered and the reliability of the film is not high, the electron beam and thermal evaporation process are often considered. Another advantage of the thermal evaporation process is that a wide range of evaporation materials can be selected, from metal materials to semiconductor materials to dielectric materials; It can be used from fluoride to oxide.
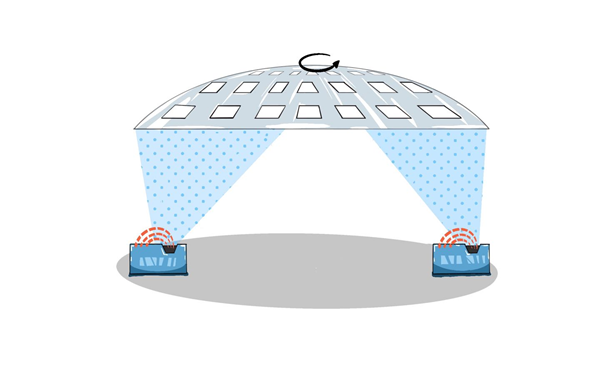